Liquid Filtration for Pharmaceutical Manufacturing
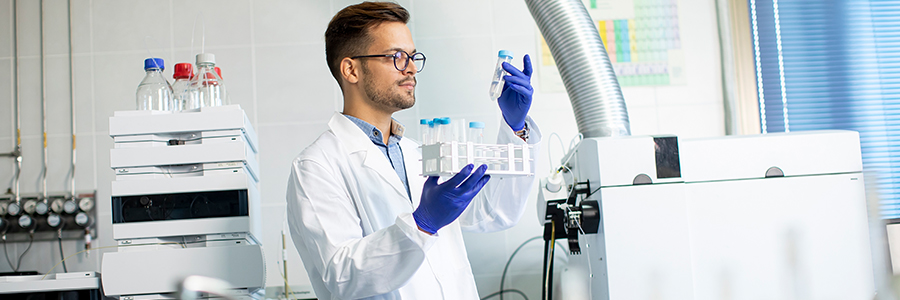
Pharmaceutical manufacturing involves a crucial process known as liquid filtration, which aims to remove impurities and particles from liquids like water, buffers or solvents. The goal is to ensure the final product is safe for human consumption. That’s why filters are utilized in pharmaceutical manufacturing.
The reasons why pharmaceuticals require filters are numerous. The primary role of filters is to eliminate contaminants from liquids, including bacteria, viruses and other microorganisms that can seriously threaten human health. By removing these contaminants, filters ensure the end product is safe for consumption.
Additionally, filters can help remove particles from liquids, such as dust, dirt and other debris, that can affect the quality of the final product. Filters also play a vital role in ensuring that the final product is pure and meets the required standards by effectively eliminating these particles.
Besides removing contaminants and particles, filters can also help separate different liquid components. For instance, filters can help separate water from solvents or different types of solvents from each other in pharmaceutical manufacturing. This is essential since different components may need to be combined in specific ratios to achieve the desired final product.
The importance of filters in biopharma
Filters are vital in the biopharmaceutical industry owing to their significance in the purification and processing of pharmaceutical products. As a result, it is essential to choose the right filter, as a wrong one can lead to product contamination, loss of yield and compromised efficacy.
The filter choice will depend on the type of product being processed, the desired purity level and the filter material’s specific characteristics. The biopharmaceutical industry uses many filters, including membrane, depth and cartridge filters.
Membrane filters are commonly used to remove microorganisms and particles, while depth filters effectively remove contaminants from larger liquid volumes. Cartridge filters are used in high-flow applications and can remove various impurities, including bacteria, viruses and endotoxins.
Selecting the appropriate filter for a specific application requires carefully considering the filter’s pore size, material composition and compatibility with the drug solution. Filters are designed to remove contaminants without affecting the drug’s purity or activity, so the choice of the filter must be based on specific product characteristics. The filtration in the pharmaceutical industry is divided into various types depending on their use and relevance.
Types of filtration systems used in the pharmaceutical industry
The pharmaceutical industry relies on a range of filtration systems, each offering distinct benefits and ways to address specific limitations. As a result, they play a crucial role in maintaining product quality and safety. The different filter systems are described in detail below.
Ultrafiltration
Ultrafiltration is a membrane filtration type that separates particles based on size. It separates macromolecules and polysaccharides from small molecules. The ultrafiltration system is particularly useful for purifying biological molecules and concentrating dilute solutions.
Surface Filtration
Surface filtration is a type that captures particles on the surface of a filter medium. This filtration type finds its applications in the pharmaceutical industry to remove contaminants such as bacteria, fungi and viruses from liquids and gases. Surface filters are designed from various materials, including ceramic, polypropylene and glass fiber.
Depth Filtration
Depth filtration captures particles throughout the filter medium’s thickness. It is often used to remove particulate matter and endotoxins from liquids. Depth filters utilized for this process are made from cellulose, diatomaceous earth and activated carbon.
Crossflow Filtration
Crossflow filtration utilizes tangential flow to separate particles from a liquid or gas stream. In this method, the liquid or gas flows parallel to the surface of the filter medium, creating a shear force that separates particles from the filter. Crossflow filtration is particularly useful for separating particles that are otherwise difficult to capture using other methods, such as colloids and emulsions.
Microfiltration
Microfiltration separates particles based on the size of 0.1 to 10 microns. It removes bacteria and yeast from liquids to clarify and sterilize pharmaceutical products. This relatively gentle method does not damage delicate molecules, making it perfectly suitable for use in the pharmaceutical industry.
To sum up, the choice of filtration system depends on the specific requirements of the pharmaceutical process, such as the size and type of particles to be removed, the desired purity of the final product and the volume of material to be filtered. Filters are also used for pharmaceutical filtration/processing, similar to filtration systems, depending on the operation or process.
Filters used for pharmaceutical filtration / processing
Pharmaceutical filtration and processing rely on various filter types, each carefully designed to meet stringent quality standards, ensure optimal product purity and safeguard patient safety. Here are some common types:
Depth Filters
Depth filters clarify liquids, reduce particles and remove microorganisms. These filters are made from cellulose, diatomaceous earth and activated carbon. The filter medium has several inches of depth, allowing for high dirt-holding capacity.
Membrane Filters
Membrane filters sterilize liquids, remove particles, and separate different components in a mixture. They are made from nylon, polyethersulfone, and polyvinylidene fluoride. These filters have precise pore sizes ranging from 0.02 to 10 microns.
Cartridge Filters
Cartridge filters are used for various applications, including removing particles and microorganisms from liquids and gases. They comprise a cylindrical housing and a replaceable filter element. The filter element of cartridge filters is designed using materials such as polypropylene, fiberglass and polytetrafluoroethylene.
Bag Filters
Bag filters are used for removing particles from liquids and are made from nylon, polyester and polypropylene. They consist of a bag-shaped filter medium that is enclosed in a housing. Bag filters are typically used for high-flow applications.
Activated Carbon Filters
Activated carbon filters remove impurities such as organic molecules and chlorine from liquids and gases. They are made from activated carbon, which has a large surface area to adsorb impurities. These activated carbon filters are often used in water purification systems and the production of pharmaceuticals.
To sum up, the filter choice depends on the specific application and the impurities that need removal. Choosing the right filter ensures the final product’s quality and purity. However, knowing how liquid filtration works is important to conduct the pharmaceutical processes.
How liquid filtration works in the pharmaceutical process
Liquid filtration is an essential step in pharmaceutical manufacturing, as it ensures the final pharmaceutical product’s safety, quality and efficacy. In addition to separating the impurities from the liquid to obtain a pure and clear product, here are the steps involved in liquid filtration in the pharmaceutical process:
Selection of the Filtration Method
The first step involves selecting the appropriate filtration method based on the properties of the liquid being filtered, the type of impurities and the desired level of purity. Several filtration methods are available, including membrane, depth and adsorptive filtration.
Pre-Filtration
Before filtration, the liquid is pre-filtered to remove large particles and debris that could clog the filtration system. This is typically done using a coarse filter, such as a strainer or a filter bag.
Main Filtration
The pre-filtered liquid is then passed through the selected filtration method. In membrane filtration, the liquid is passed through a membrane with small pores that trap impurities.
Depth filtration uses a porous material, such as diatomaceous earth or activated carbon, to trap impurities. Adsorptive filtration involves using materials that attract and bind impurities, such as activated carbon or ion exchange resins.
Post-Filtration
Once the liquid is filtered, it undergoes post-filtration to ensure that all impurities have been removed. This step involves passing the filtered liquid through a final filter with a smaller pore size than the main filter to capture any remaining impurities.
Cleaning and Sterilization
Finally, the system is thoroughly cleaned and sterilized after filtration to prevent contamination in subsequent cycles. This involves flushing the system with cleaning agents and disinfectants and subjecting it to high temperatures or radiation.
As discussed above, filtration systems work perfectly with the right type of filter. That’s why knowing which filter to choose for your pharmaceutical process is important.
Selecting the right filter for your pharmaceutical process
In the pharmaceutical industry, selecting the appropriate filter is critical to ensure the final product’s safety, efficacy and quality. Filters are used to remove impurities, contaminants and particles from liquids and gases during the manufacturing process and to maintain the integrity of the product. Below are some factors influencing the selection of the right filter for your pharmaceutical process:
Filter Material
The filter material is important in pharmaceutical filtration for various reasons, such as compatibility with the filtered product, preventing product contamination, avoiding impurities and abiding by regulatory compliances. Some common filter materials include polypropylene, nylon, cellulose and PTFE.
Pore Size
The pore size of the filter is also critical, as it determines the size of particles and contaminants that can be removed from the liquid or gas. The appropriate pore size should be chosen based on the size of the particles that need to be removed.
Filter Type
Each filter type, such as depth, membrane and cartridge, has its benefits and limitations, and the appropriate filter type should be chosen based on the specific requirements of the process.
Flow Rate
The filtered product’s flow rate is also important when selecting the filter, as it ensures cost-effectiveness, maintains product quality, meets production demands, optimizes filtration system capacity and avoids production delays. The filter should be able to handle the required flow rate without compromising the quality of the final product.
Regulatory Compliance
Pharmaceutical processes are subject to strict regulatory compliance requirements. The selected filter should comply with all relevant regulations and standards to ensure the final product is safe and high-quality. Some of these regulatory requirements are listed below:
Good Manufacturing Practices: GMP regulations ensure that pharmaceutical products are consistently produced and controlled to meet quality standards. Filters used in pharmaceutical processes must comply with GMP guidelines, including documentation requirements, equipment qualification, validation, traceability and quality control.
Pharmacopeial Standards: Pharmacopeias, including United States Pharmacopeia (USP) and the European Pharmacopoeia (Ph. Eur.), set standards for the quality, purity and performance of pharmaceutical products. These standards often specify the types of filters, materials and pore sizes that should be used for specific applications, such as sterilization or particulate removal.
Regulatory Guidelines for Particulate Matter: Various regulatory bodies, such as the FDA, have guidelines specifying acceptable limits for particulate matter in pharmaceutical products. Filters used for particulate removal must be selected to achieve the desired level of cleanliness and comply with these limits.
Validation and Documentation: Filters must undergo validation processes to demonstrate their suitability for the intended application. This includes validating their ability to remove contaminants and ensuring compatibility with the product and consistent performance. All validation activities must be documented to comply with regulatory requirements.
These regulations ensure that the filter must be chosen carefully to meet the specific requirements of regulatory bodies. The filter should perform effectively in removing impurities and comply with the documentation, validation and quality control procedures required by regulatory agencies.
Besides the manufacturing processes, Avantor offers a range of products and services to support your research and development. From high-quality filter materials to advanced purification technologies, Avantor ensures regulatory compliance and product integrity.